How offsite technology is transforming UK construction
Offsite technology has improved significantly over the last 5-10 years as has the sector’s ability to manage the delivery of these projects with the least disruption possible. The modular sector is now much more mature, and the technical and project management capabilities among the leading offsite specialists have advanced hugely – to the benefit of clients and contractors needing high quality, fast-track solutions.
There is now much greater confidence in the ability of offsite manufacturers to deliver high quality building solutions rapidly – whether for temporary or permanent facilities – and in every sector, from education and healthcare to residential, commercial and infrastructure.
Building Offsite Drives Productivity
As offsite specialists have embraced lean manufacturing techniques, productivity has increased. The sector is simply doing things better. This means even shorter lead times for both temporary modular facilities, and bespoke buildings and extensions.
Manufacturers have widened their skillsets and improved project management and BIM capabilities, giving construction clients much greater assurance of delivery on time, to reduced programmes, stringent quality standards and with the least disruption possible.
How as the Covid-19 Pandemic Impacted on the Offsite Sector?
The offsite sector most definitely switched up a gear to help the NHS and the Government respond to the crisis. Collaboration across the supply chain has been unprecedented and there has been genuine partnership working to deliver numerous projects to the most incredible timescales.
We saw this very clearly on the NHS Nightingale Exeter project we worked on with BAM. The programme time for the new hospital was reduced from about 12 months to just 57 days which could not have been achieved with a traditional contractual way of working.
There was a tremendous ‘can do’ attitude across the board, with the main contractor, modular supplier, fitout, and M&E specialists working closely as one genuine team.
The same approach was adopted for the rollout of the Covid-19 testing sites. We brought together a range of suppliers to help us deliver fully-serviced community testing centres. We installed up to three sites per week, from Inverness to Portsmouth, and were on site for just 2-3 days, often handing over sites just a week after initial notification. This really was a phenomenal achievement.
The pandemic definitely shone a spotlight on the offsite sector. It has raised awareness of what is possible with a higher level of collaboration and partnership working.
We have been saying for years that offsite construction offers much greater certainty of delivery and reduced risk. The fact that our factories continued to operate safely and at capacity from the very start of the pandemic is further evidence of this.
Helping to Address the Challenges Facing UK Construction
The shortage of skilled labour is now even more severe following Brexit and the Covid19 pandemic which means more clients and contractors need to turn to offsite solutions to achieve greater certainty of delivery on time and on budget.
Reducing the impact of construction by moving more work offsite and into a factory, is particularly critical on hospital and school sites and is another significant driver.
Why More Housebuilders Should Consider Offsite
The modular housing market has become more crowded, driven by skills shortages which are particularly severe in the residential sector.
Fast-track building solutions are beneficial to address shortfalls in social housing stock and move tenants off waiting lists more quickly so demand for offsite in this market will continue to rise.
Poor build quality is still very prevalent in the housebuilding sector, creating opportunities for modular homes where there is far better quality control in a factory. It is also easier to achieve the required levels of productivity and meet regulations such as fire and acoustics using offsite manufacturing.
The Future of Offsite
There are huge lessons to be learned from the Covid19 pandemic, which highlighted the need to make facilities more interchangeable and futureproof.
Offices can become wards or buildings may need to be relocated to different sites to meet changing local needs. This means assets will be considered differently whilst still needing to meet the same standards for build quality and comfort. Buildings will need to be more flexible and adaptable to change, presenting tremendous opportunities for modular construction.
We believe more buildings will be leased to reduce capital expenditure and after the leasing period, modular facilities can easily be removed, relocated, reconfigured or refurbished.
The drive to net zero also presents enormous opportunities for offsite. Modular solutions are a simpler route to achieving low or zero carbon construction and manufacturers need to be leading the way in this area.
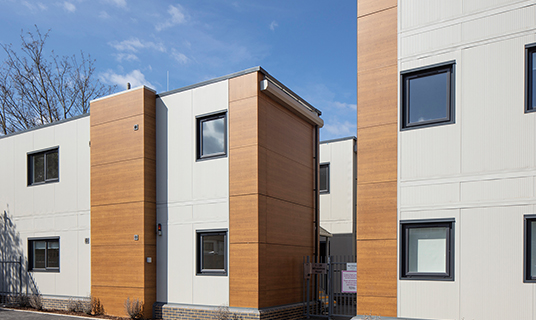